Wesleyan Labs Create, Donate Face Shields to Local Hospital
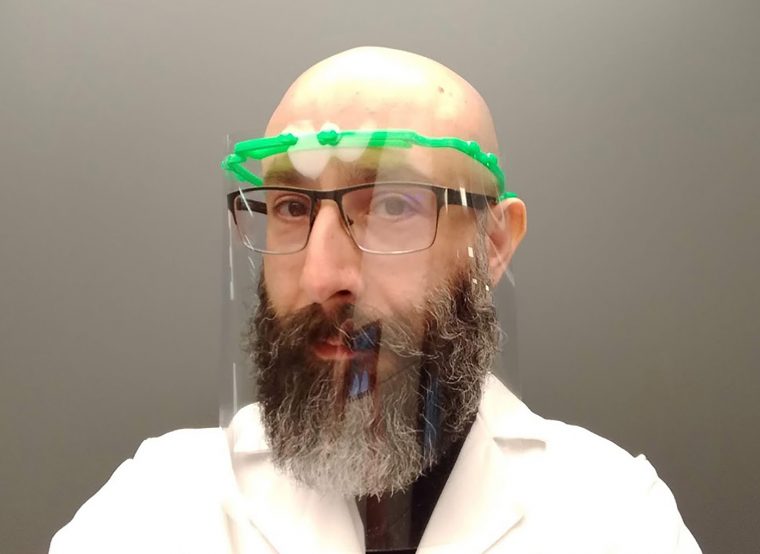
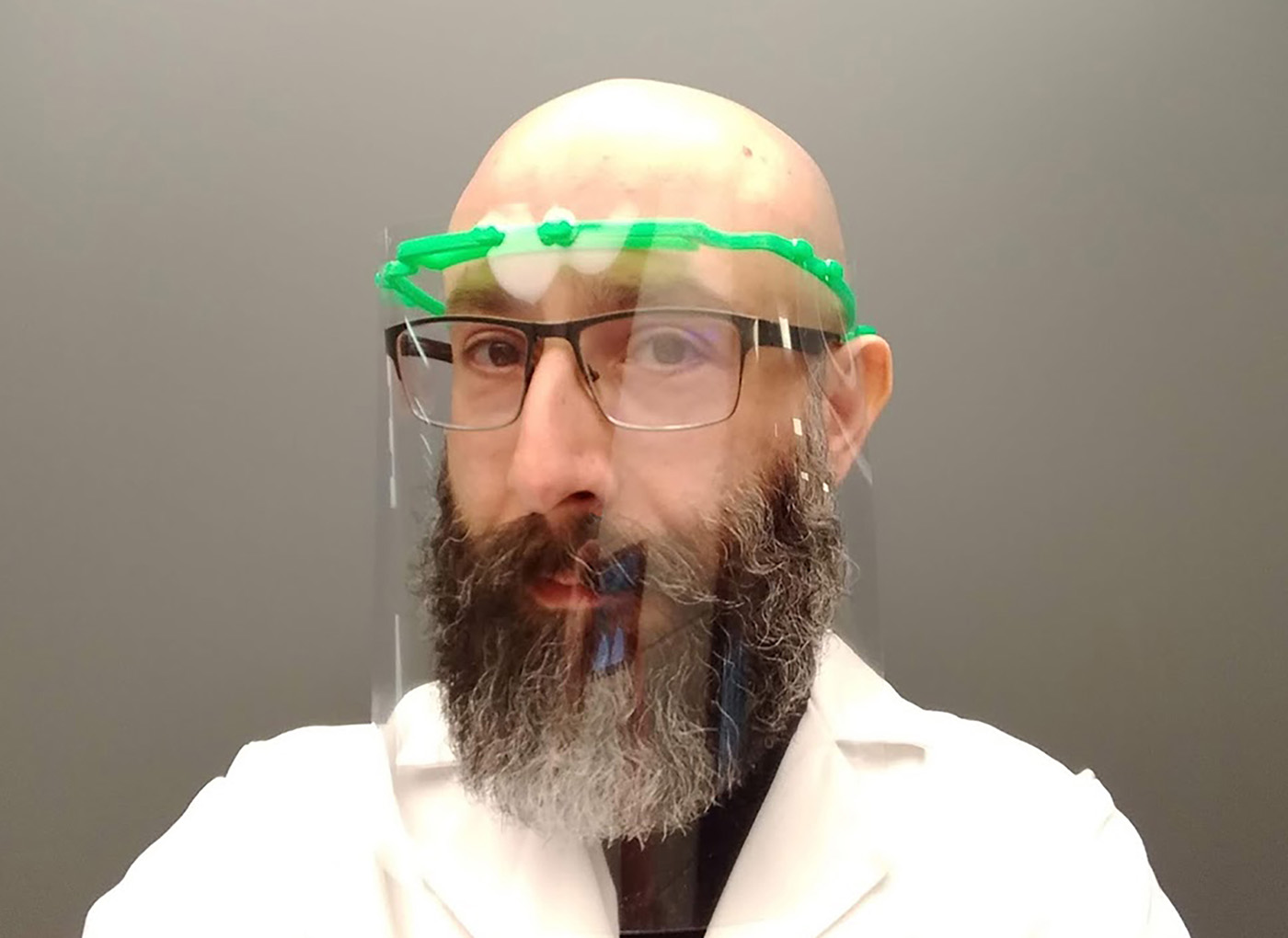
To help medical personnel safeguard themselves during the coronavirus outbreak, two makerspace labs on campus are manufacturing much-needed protective masks using 3D printers.
On April 1, Wesleyan donated its first set of 100 face shields to medical personnel at Middlesex Hospital in Middletown, and others to Wesleyan staff who must work on campus to support the remaining students. The mask, which offers a barrier from the spray of liquids, can be used with or without additional medical masks that cover the nose and mouth.
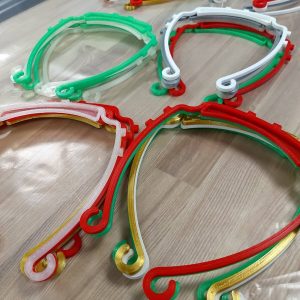
“Our 3D printers have been running at full speed,” said Francis Starr, professor of physics and IDEAS (Integrated Design, Engineering, and Applied Sciences) program coordinator.
Shawn Lopez, the IDEAS Lab coordinator, initiated the project at Wesleyan after “weighing the potential benefits (vast) against the potential harm (nonexistent).”
“Designs for hand-sewn masks and 3D-printed visors were making the rounds on makerspace blogs and websites. It was clear that we could jump in and make a difference here at Wesleyan,” Lopez said. “As the coordinator of the lab, I understood that it was within my purview to undertake a project of this nature.”
The IDEAS Lab is building a full-face protective visor based on a design by 3DVerkstan in Stockholm, Sweden. The Verkstan masks require only a 3D printer, filament, a semirigid clear plastic, and a hole punch to build.
“The advantages of the Verkstan model were the speed of printing (less than an hour per visor mount), the relatively low amount of filament required (approximately 20 grams per mask), the ease of procuring the shields to go along with the mounts (available at local stores and modified with a three-hole punch) and the overall simplicity of the design,” Lopez explained. “One hundred pieces can ship in a tiny box as separate components and can be assembled in less than 30 seconds. Many other designs can’t be shipped as easily, take a long time to print, and require up to 10 times as much filament per piece.”
Chris Chenier, adjunct assistant professor of art and digital design technologist, is using six 3D printers in Wesleyan’s Digital Design Studio to print similar masks. So far, he’s printed 85.
“I tend to average 18 headbands per day,” Chenier said. “Obviously, there’s so much need out there and demand continues to grow for PPE. Our current pace feels manageable, as so many of us are splitting time between working at home, trying to keep our remote students engaged, and supporting our families and neighbors. For me, the stress and chaos of the last few weeks is more manageable because of this project. It’s been really good to have something positive to contribute.”
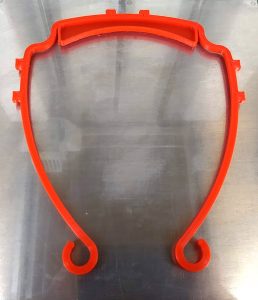
Daniel Moller, assistant professor of the practice in integrative sciences, is producing copies from his 3D printers at his home.
“I thought I could add to the volume of output (even if by a small amount) since I can care for and feed my printer for longer hours if I’m at home,” Moller said. “My printer is set up next to my son’s gaming area, so between him (who I’ve trained to remove, prep, and restart prints) and me, we have just been tending it as frequently as possible throughout the waking hours. We were able to make more than 30 over the course of a long weekend, which is pretty good.”
Unfortunately, the number of requests from health care providers is already exceeding the capacity of Wesleyan’s two makerspaces.
“As a result, donations are being prioritized to protect essential Wesleyan staff, Middlesex Hospital, and Middletown Healthcare Partners. Any excess supply will be donated to other local health providers,” Starr said.
The next 50 masks will go to Wesleyan’s Bon Appetit employees who continue to cook and serve food to the nearly 250 students remaining on campus. Another 50 will go to the essential personnel working in Physical Plant-Facilities.
“We’ll continue to produce and distribute to the folks in need, beginning with the home team and moving outward from there,” Lopez said.
On its website, the IDEAS Lab offers suggestions and directions for creating various protective masks, using tools that range from simple scissors or a sewing machine to a 3D printer or laser cutter.
“Personally, I have a tendency to throw myself into things like this,” Lopez said. “I can’t just watch events happen, especially knowing there’s an option to get involved. I was so happy to find a project that could potentially make such a difference. It galls me to no end to see that it is necessary, but this is the reality we’re all facing.”
Wesleyan President Michael Roth ’78 also blogged about the IDEAS Lab’s efforts on March 31, in a post titled “Making Face Shields in the Crisis.”