New CoGen System Generating 81 Percent of Electricity
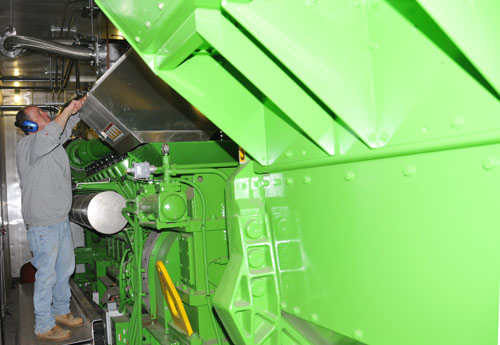
It’s one mean, green machine and it’s saving Wesleyan up to $5,000 a day in energy costs.
Wesleyan’s new Cogeneration system – or CoGen, – uses natural gas to simultaneously generate electricity, heat and steam for university use. It began operation in February after an 18-month installation process.
“Buying electricity from the grid is expensive and non-efficient,” says Peter Staye, associate director of utilities management. “With CoGen, we are generating 81 percent of our own power. It should pay for itself in five years.”
CoGen operates similar to a vehicle with an extreme super-duty engine. The natural-gas fired, turbo-charged, four-stroke engine runs on 16 cylinders. Each cylinder is 5.8 liters. (A 2009 Ford F-150 has eight cylinders with a 4.6 liter engine.)
Made by General Electric in Austria, the 22,000-pound Jenbacher gas engine runs at 1,500 revolutions per minute. It powers a generator, which ultimately creates 2,398 kilowatts of electricity.
Staye offered a comparison of two recent electric bills side by side. In February 2008, Wesleyan consumed 1,558,687 kilowatt hours. In February 2009, with CoGen in operation, the usage dropped to 359,584 hours. Monthly electric bills have dropped from the $180,000 range to under $50,000.
“By generating our own power, we’re saving Wesleyan up to $5,000 a day in electricity costs,” Staye says.
This will be especially useful in the summer when Wesleyan uses an average of 65,000 kilowatt-hours of electricity a day to power 90 buildings on campus.
CoGen not only generates electricity, but uses its “wasted” 800-degree heat to make steam and hot water for university use. High Rise residence hall and the Central Power Plant are heated with the thermal energy from the engines cooling system during the winter months and the campus steam loop receives 3,000 pounds of steam per hour year round from the energy in the engine’s exhaust.
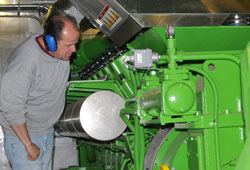
“Conventional power plants emit the heat created as a by-product in to the environment. We’re using a waste product from the engine to make our own steam,” Staye says.
Gary Yohe, the Woodhouse/Sysco Professor of Economics, is an expert on the potential damage of global climate change. He applauds Wesleyan for installing a cogeneration system.
“Wasting energy is never good for the planet so when CoGen works out, it’s good for the bottom line and great for the planet,” Yohe says. “When you burn a ton of fossil fuel, you can waste 75 percent of the energy it makes. If but you have the ability to only waste 50 percent, that is reducing the carbon footprint by a third, and that is substantial.”
Like any vehicle engine, CoGen’s exhaust is toxic. It contains carbon monoxide, nitrogen oxides and carbon dioxide. To reduce emissions from the engine’s combustion, the exhaust is mixed with a non-hazardous solution of urea, rich in ammonia. The mixture then enters a chamber full of honeycomb-patterned platinum plates and serves as a selective catalytic reactor.
As the exhaust passes through the reactor, a chemical reaction occurs that causes the emissions to break down.
“The nitrogen in the ammonia combines with nitrogen oxides in the exhaust and the resulting gas, now much cleaner, is a combination of nitrogen, oxygen, water vapor and carbon dioxide,” Staye explains. “The process works much the same way as a car’s catalytic converter, but on a much larger scale and with greater precision.”
Wesleyan is producing half of the permitted emissions allowed by the Environmental Protection Agency.
“We’re still making Co2 but the rest of the exhaust stream is very clean,” Staye says.
CoGen cost $4.5 million to install, however a grant from the Connecticut Department of Public Utility supported $1.6 million of the bill. In return, Wesleyan runs the system 24/7 and has agreed to run CoGen from noon to 8 p.m. June 1 through Sept. 31 and Dec. 1 through Jan. 31 to help reduce loads on the regional electrical grid. CoGen’s annual maintenance bill runs about $250,000.